Moxa Connectivity Solutions for COVID-19 Problems
Jun 09, 2020
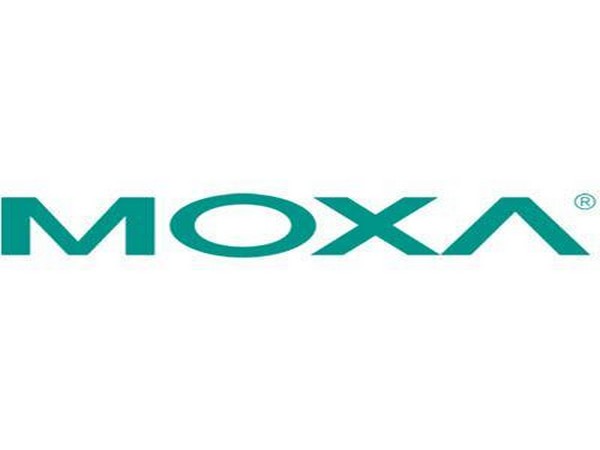
Bengaluru/Taipei, Taiwan, June 9 (ANI/PRNewswire): The COVID-19 pandemic is posing a considerable challenge for industries worldwide, and Moxa is helping both small and large enterprises implement short-term preventative measures, business continuity plans, and revival growth plans that will help after the COVID-19 pandemic.
The attempts to slow the spread of COVID-19 have resulted in many disruptions to business and daily life. As the health and safety of their customers, employees, vendors, and communities are important to them, the company's thoughts are with everyone during this difficult time. Moxa understands the responsibilities their partners and customers still have to handle and would want to let them know that they are running as usual and that they can be relied upon.
With the number of remote workers has reached the millions in Europe and the US and is in the hundreds of millions in China, the pandemic has fundamentally transformed the way many businesses operate. Educational institutions are adopting virtual classrooms and distance learning, online shopping sales are exhibiting considerable increases, and even online gaming is witnessing a marked increase in the number of users.
For manufacturing industries, digital transformation has become crucial. In the long run, this situation may accelerate, or even necessitate, a major shift toward the digital transformation of industrial automation.
Reconsidering Operational Transformation
The first short-term consideration for enterprises is how to respond internally to social distancing measures. At Moxa, they have been closely monitoring the COVID-19 situation and have taken measures to ensure the safety and health of their staff. These measures include moving away from face-to-face meetings and utilizing modern communication tools to facilitate work, meetings, and remote collaboration. These same measures have become commonplace around the world.
Given the urgency with which enterprises must respond in order to survive, the second consideration is how to speed up the implementation of digital technology, particularly in production. Traditionally, this ability has been thought to be reserved for larger enterprises with high-variety/low-volume production models, yet being able to develop the flexibility that digital production lines afford may be critical to business survival, especially in the face of the COVID-19 pandemic.
These changes can affect operations and budgets. The flexibility and capability of digital production lines, however, can give enterprises the ability to switch their end products in order to meet shifts in market demand. In the current environment, for example, LVMH have been able to switch their perfume and cosmetics production to medical detergent and disinfectant, while Ford and GM have utilized their automotive assembly line to produce face masks and ventilators. Other industry giants, such as Dyson and Foxconn, have also been able to leverage existing technology to produce air purifiers and face masks.
Automation for COVID-19 and Beyond
While many short-term changes are expected to focus on cutting back operating and human resource costs, increasing efficiency, and switching production, it is critical for such changes to have long-term benefits. For viable, long-term automation solutions, plans should be aimed at upgrading existing equipment to increase production efficiency, reduce maintenance costs, and minimize equipment failure.
In this regard, remote monitoring and maintenance are key solutions that have become essential tools with long-term benefits. With the 'work-from-home' model that has been widely implemented to continue operations safely, Moxa has assisted businesses with upgrading their systems quickly and securely. Even though remote maintenance is able to provide faster troubleshooting, there remains a strong preference for maintenance engineers to investigate problems on-site. However, the current situation has forced many businesses to realize that secure remote access can help to reduce onsite visits, improve services and increase operational efficiency while saving time and costs.
With nearly 35 years of experience in constructing communication networks, Moxa has observed that overcoming barriers to operational transformation often requires enterprises to partner with experienced solution providers to handle the many complex issues that can arise, and this is especially the case for smaller or less-experienced businesses. Of particular importance, Moxa's experience has enabled them to develop multiple secured network solutions that allow businesses to operate more efficiently and with peace of mind that their data is secure.
Moxa is doing its best to make this challenging period as smooth as possible for all parties involved. They hope that they can return to their normal lives as soon as possible and appreciate the stakeholders bearing with them until then. In the meantime, please feel free to reach out to contacts at Moxa at any time to communicate needs. Health and safety are of critical importance. Stay safe, stay healthy, and take care.
This story is provided by PRNewswire. ANI will not be responsible in any way for the content of this article. (ANI/PRNewswire)